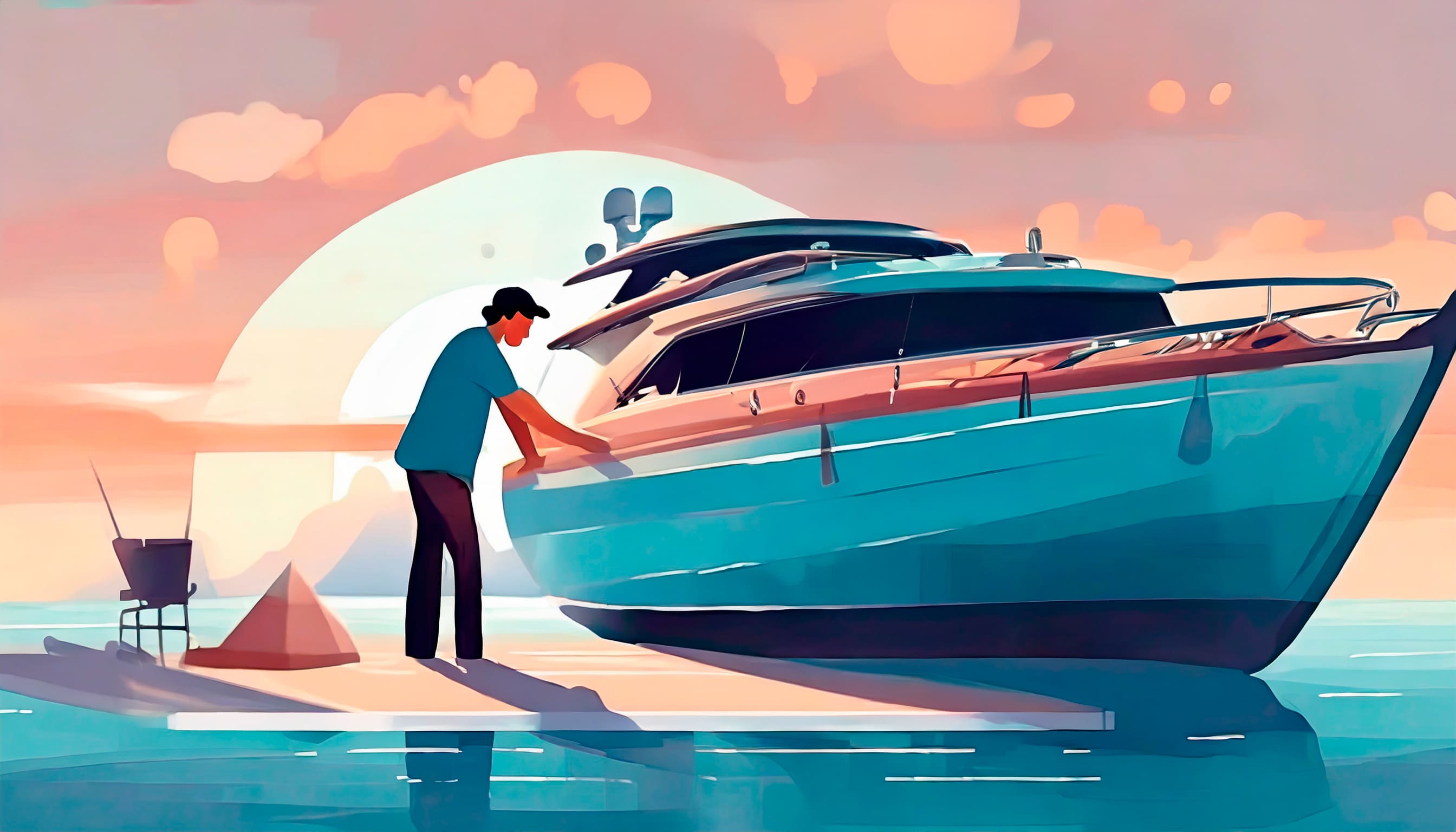
How are motorboats made? A detailed guide from sketch to sea
The craft of motorboat building has evolved remarkably over the years, shaped by technological advances, innovation, and changing maritime needs. Yet, amidst this whirlwind of progress, certain core principles have stood the test of time.
Precision is among the enduring cornerstones, essential for ensuring both the safety and high performance of each vessel. It goes hand-in-hand with craftsmanship, a blend of skill, experience, and artistry that holds its ground even amidst technological leaps and automation. Expert dexterity and knowledge are indispensable in tasks such as hull shaping, woodworking, and detailed finishing - areas where machines can't match the human touch.
Above all, the continuous pursuit of improvement anchors this industry, consistently pushing limits to enhance speed, stability, and comfort. This guide seeks to illuminate this complex process, exploring how these fundamental elements have been preserved and adapted in the evolving landscape of boat building, from the initial design conception to the point of purchasing the motorboat.
History and evolution of motorboat building
The motorboat industry was born from humble origins, with early designs surfacing in the late 18th century. Among the first ones was the Pyroscaphe, a steam-powered vessel that sailed the Saône in 1783. These trailblazing machines, while innovative, presented numerous challenges, including managing heat and pressure control and bearing their size and weight on the vessels. Concurrently, these pioneering crafts were predominantly wooden; a material that was both abundant and workable. It allowed for structure diversity but presented issues of durability and efficiency.
With the advent of internal combustion engines in the late 19th century, the industry experienced a significant shift. Boats became smaller and more powerful, and their construction materials evolved. Incorporating steel, and subsequently aluminium and fibreglass, provided better durability, lighter weight, and resistance to water damage.
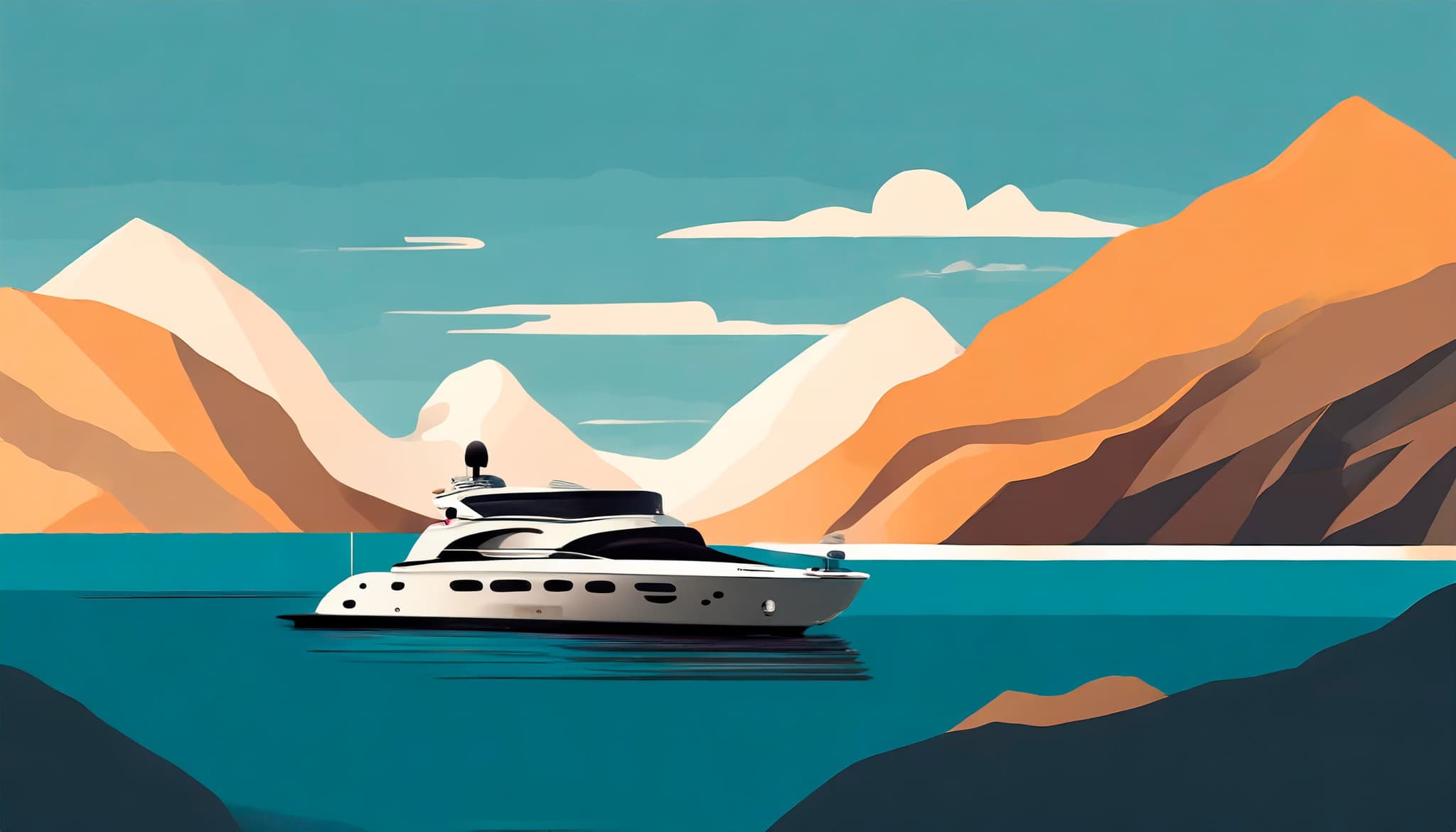
Into the 21st century, motorboat construction has become a blend of artistry and technology. Computer-aided design and manufacturing (CAD/CAM) tools have enabled precise and complex designs, boosting efficiency and performance. Materials have further evolved, with composites and advanced polymers offering enhanced strength and weight properties.
The role of technology in different types of motorboats
The influence of technology is profound in how motorboats are made, shaping the industry's future and continually raising the bar for what can be achieved. Computer-aided design and manufacturing systems (CAD/CAM) are foundational across all boat-building classes, from speedboats to fishing vessels. These systems facilitate the creation of efficient, custom designs and precise manufacturing of complex geometries.
Modular construction methods and laser-guided alignment systems are also increasingly utilised, especially in larger vessels such as yachts, ensuring precision and structural robustness. Moreover, digital templating tools quicken the fitting-out process, delivering a high degree of customisation and accuracy.
Industry 4.0 technologies, like IoT, robotics, and AI, are becoming ubiquitous, automating labour-intensive tasks, enhancing quality control, and optimising resource use in boatyards. They also enable efficient integration of complex systems, from luxury yachts' electrical networks to fishing boats' sonar systems (which use sound waves to detect underwater objects).
How motorboats are made: From concept to blueprint
The creation of a motorboat begins with an idea, a vision often born from a blend of consumer needs, engineering insight, and artistic creativity.
Here is the progression from the initial inception to the meticulously detailed final blueprint:
Initial sketches and digital design: Every boat starts its life as a concept or a sketch. Designers draw preliminary drafts, capturing the broad shape and aesthetics of the vessel. This vision is then translated into a more precise digital model using CAD software - a technology that allows creators to create 3D models, modify designs with ease, and experiment with various configurations.
Hydrodynamic and structural analysis: Once the preliminary digital model is ready, the next step involves rigorous hydrodynamic and structural analysis. Using Computer-Aided Engineering (CAE) tools, engineers simulate the boat's behaviour in various water conditions and evaluate its seaworthiness, stability, and performance. These analyses inform crucial adjustments to the hull design, improving the boat's efficiency and safety.
Selection of the right motor and propeller: The boat's engine and propeller are crucial components that significantly impact its performance. The choice of motor depends on the boat's intended use, size, and weight, among other factors. Likewise, the propeller must be chosen with care, considering its diameter, pitch, material, and the number of blades, to ensure optimal propulsion and fuel efficiency.
Finalising the blueprint with precise measurements: Following the design adjustments based on analyses and motor selection, the final stage of the process involves refining the digital model into a detailed blueprint. This provides precise measurements for every boat component, from the hull and deck to the most minor fitting. It serves as the definitive guide for the construction phase, ensuring the boat is built to exact specifications.
What are motorboats made of? Material selection and preparation
The quality of materials selected for boat construction profoundly impacts the motorboat's longevity and performance. The strength of a hull braving harsh sea conditions, a propeller's seamless cut through waves, or the boat's endurance during off-season storage, all hinge on this crucial choice. Similarly, it informs interior aesthetics, comfort, and functionality.
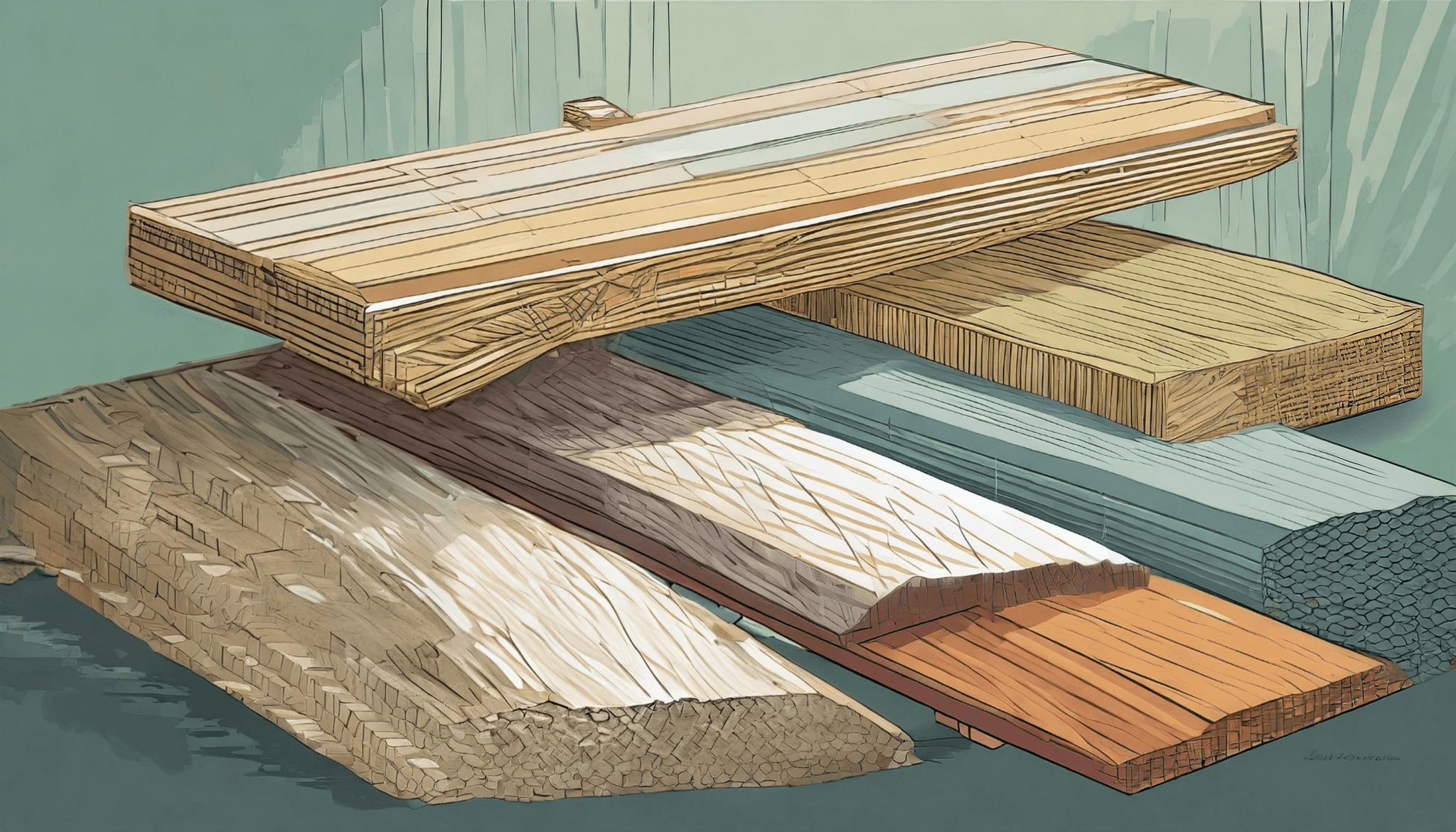
Fortunately, today's advancements introduce a spectrum of materials, each abundant in properties and benefits. Here is a deeper understanding of some of the most widely used, their roles and distinct benefits in boat construction.
Material | Boat parts | Why it's used |
---|---|---|
Fibreglass | Hull, deck | Strong, lightweight, and resistant to corrosion and water damage |
Carbon fibre | High-performance hulls, decks, masts | Extremely strong and light; allows for more speed and efficiency |
Steel | Hull (larger vessels), keels | Strong, durable, and easily repairable; good for large structures |
Aluminium | Hulls (small to medium vessels) | Lightweight, strong, resistant to corrosion, and easy to work with |
Wood | Traditional hulls, interiors, decks | Classic aesthetic, easy to work with, buoyant |
Rubber | Inflatable sections, seals, propeller shaft | Flexible, durable, water and impact resistant |
Plastics (PVC, Polyethylene) | Small boats, fittings, electrical insulation | Versatile, lightweight, cost-effective, and resistant to corrosion and UV light |
The process of selecting and preparing materials for boat construction is a thorough one. It involves careful evaluation of the types of motorboat, intended use, desired characteristics, and specific material properties. For instance, a high-performance speedboat may favour carbon fibre for its lightweight strength, while a fishing boat might prefer fibreglass for its durability and resistance. When it comes to the preparation, this typically includes:
Procuring the raw materials.
Verifying their quality.
Shaping them into the required forms, such as sheets for hull construction or rods for masts.
Motorboat hull construction
Hull construction starts with creating a mould shaped to the boat's final design. Layers of materials, such as fibreglass or carbon fibre, are then applied, with resin acting as a binding agent. Once cured, this forms a robust structure. Further layers may be added for reinforcement, particularly around the keel, chines, and strakes. Internals like bulkheads and stringers are integrated for additional strength. After final curing, the hull is released from the mould, revealing a strong, seaworthy vessel ready for the subsequent stages.
Crafting the deck and superstructure
The deck, much like the hull, is shaped using a mould for precision. This forms the basis for carefully laid layers of selected materials, each bonded with a resin. A steadfast commitment to accuracy underlies this process, vital to ensure an exact fit with the hull, precise placement of fittings like cleats and winches, and the seamless integration of essential motorboat safety features such as non-slip surfaces.
How are cabins on motorboats made? (The superstructure)
Next, the superstructure – encompassing the cabin and wheelhouse – is constructed. Precision remains the guiding principle, dictating the functionality and fit. Here, the earlier blueprinted internal layout comes to life, translating spaces for navigation, seating, and storage into tangible structures. This process is closely followed by cutting out window and door openings and installing necessary systems such as electricity and plumbing.
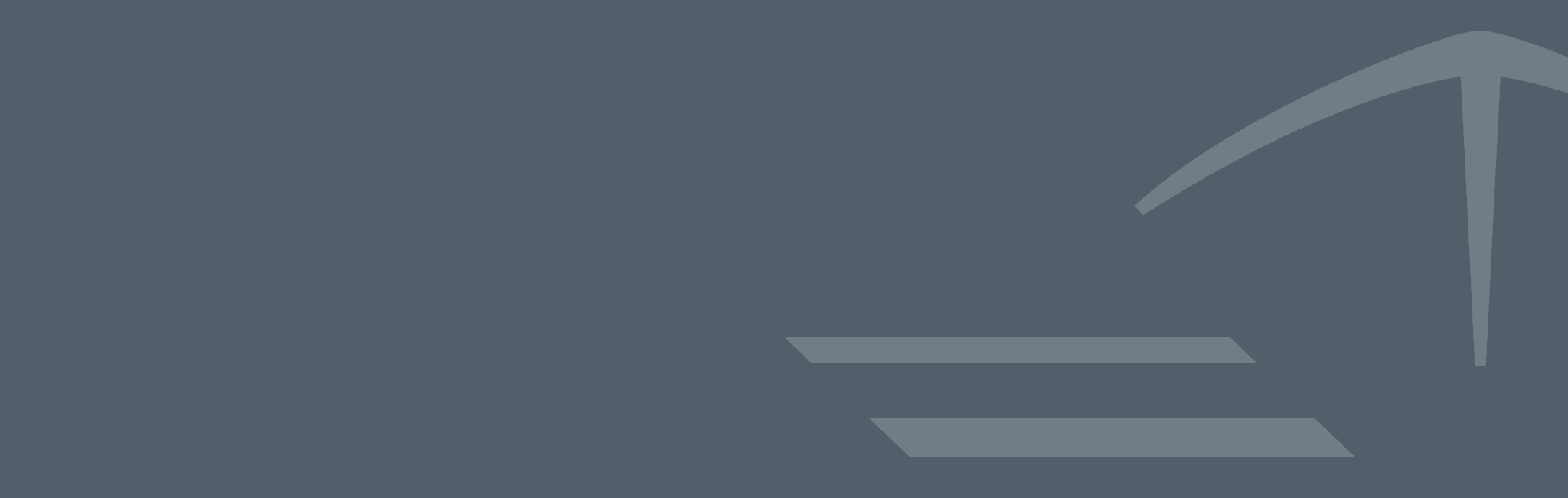
Merging deck and superstructure with the hull
The final stage involves securing the deck and superstructure to the hull. This process is often achieved through bonding and mechanical fastening and must be accurate to ensure a watertight seal and structural integrity. Following this, installations such as railings, windows, and doors are completed.
Motorboat engine and propulsion system integration
The installation and integration of an engine and propulsion system into a motorboat represent the crossroads where design and functionality merge. This step turns the static structure into a dynamic vessel, underscored by five critical stages:
Selection: The process begins with choosing the appropriate engine - often an inboard or outboard type, depending on the type of boat. An inboard engine mounted inside the hull offers balance and space optimisation. In contrast, an outboard motor provides ease of maintenance and a higher power-to-weight ratio.
Positioning: The engine's positioning within the hull impacts stability, balance, and performance. Ideally, this is centred to evenly distribute its weight, but exact placement depends on hull shape and boat design.
Compatibility check: Before installation, a compatibility check is essential to ensure all decisions made can integrate seamlessly with the boat's design and existing systems.
Installation: The engine installation involves intricate procedures, including mounting it to the hull or transom, connecting the fuel and exhaust systems, and linking the engine to the boat's controls. Measures like rubber mounting and acoustic insulation around the engine compartment are employed to minimise vibrations and noise.
Testing: Finally, rigorous trials are run to assess the system's reliability and efficiency, ensuring the power output, thrust conversion, and overall manoeuvrability meet the required standards.
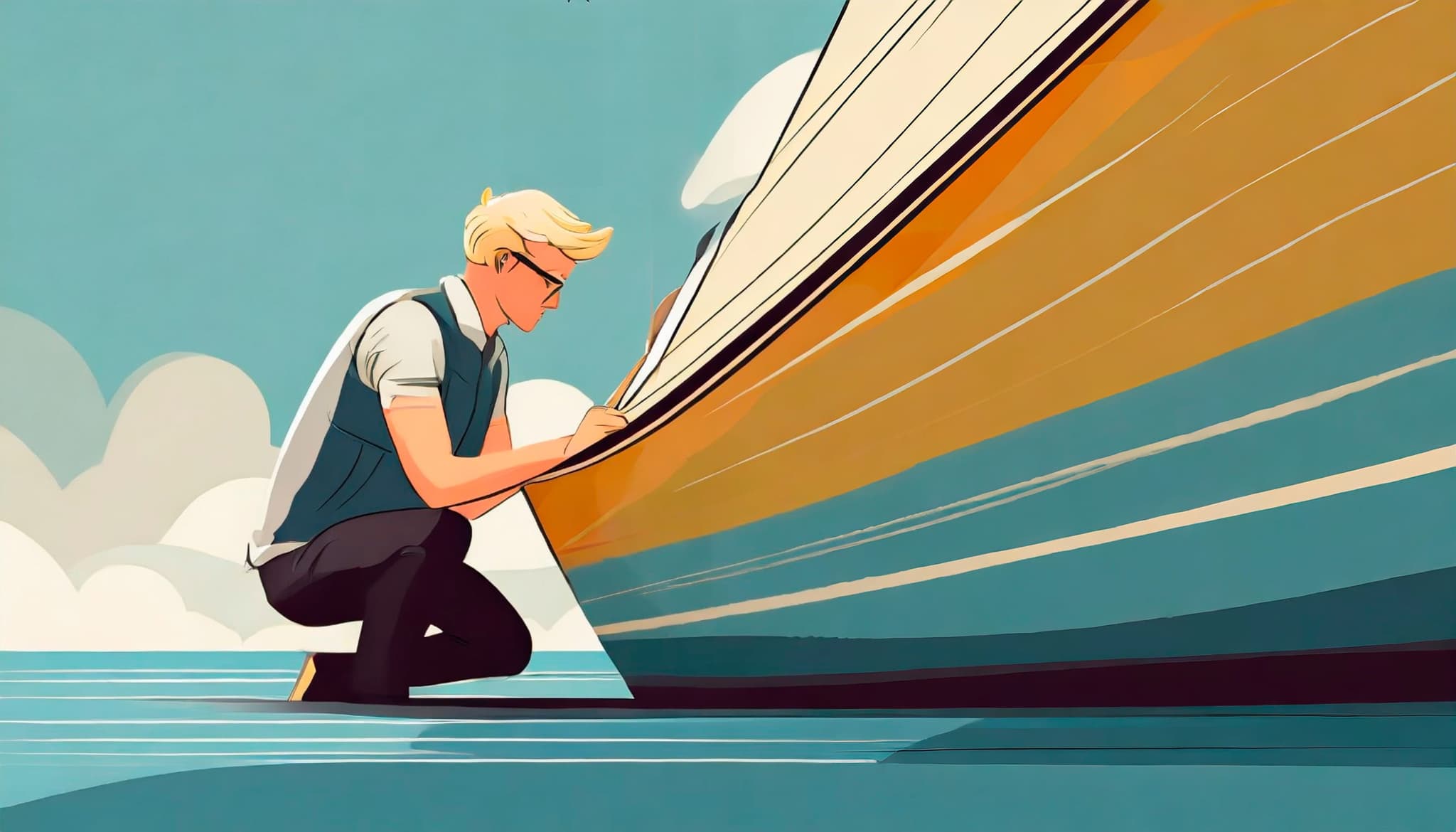
Motorboat fuel system installation
This marks an instrumental phase in the construction process, often orchestrated alongside or slightly prior to the electrical and plumbing works. Given its rigidity and safety requisites, the fuel system components - comprising tanks, lines, and pumps - are strategically placed to avoid any obstruction or interference. Adherence to safety regulations is paramount, and careful consideration of weight distribution and balance is essential to the boat's performance. This installation journey culminates in rigorous testing, aligning the system's efficiency with the boat's design, ensuring a seamless symbiosis with the engine and propulsion systems, and safeguarding the integrity of the motorboat's dynamic functionality.
Types of motorboat electrical and plumbing systems
Serving as the vital conduit of onboard functionality and safety, both at the dock and during motorboat cruises, the intricacy of electrical and plumbing systems proportionately escalates with the size of the vessel. A dual-battery setup marks the start, its redundancy powering an assortment of navigational tools, lights, pumps, and potentially appliances, all orchestrated via a circuit breaker panel. Marine-grade tinned copper wiring, colour-coded for easy identification, runs securely within the conduit. On the other hand, the plumbing system conveys freshwater through pipes to utilities like sinks and showers, propelled by pressure pumps. Critical bilge pumps expel intruding water, while the sanitation system efficiently manages waste.
How are yachts made from the inside?
The transformation from a hull to a comfortable and functional interior begins with the complex installation of structural elements, followed by fixtures, amenities, and finishing touches. Extreme precision and attention to detail ensure high-quality, durable finishes that enhance aesthetics, comfort, and practicality while thorough planning optimises space and aligns with the boat's intended use.
The level of customisation
Customisation levels in the interior installation and finishing stage can vary. Smaller, mass-produced boats usually have standard layouts, whereas larger motorboats often offer extensive personalisation, from layout options to materials and amenities. Regardless, safety regulations and the marine environment's demands must always be met.
What is the interior made of?
Motorboat interiors harness a fusion of materials, balancing durability, weight, aesthetics, and technical performance. Marine-grade plywood, known for its strength and resistance to moisture, often forms the base for flooring and partition walls. Lightweight and highly durable fibreglass is frequently used for wall linings, cabinetry, and furniture structures. Other composite materials like carbon fibre bring high strength-to-weight ratios and are crucial for maintaining boat stability and fuel efficiency. Additionally, metals like stainless steel or aluminium feature in hardware and fixtures for their corrosion resistance.
Electronics and navigation systems in motorboats
The rapid progression of marine technology continually enriches the electronics and navigation systems, creating safer, more efficient, and user-friendly boating experiences. Compact runabouts might require only basic GPS, VHF radio, and fish finders, while luxurious yachts may feature sophisticated radar, autopilot systems, depth sounders, chart plotters, and satellite communications. Integrating these components during construction ensures seamless functionality and aesthetics. System choice and complexity largely depend on the boat's purpose and size. Importantly, flexibility is built into these installations, allowing for future tech advancements and upgrades, thereby ensuring the yacht remains at the cutting edge of innovation.
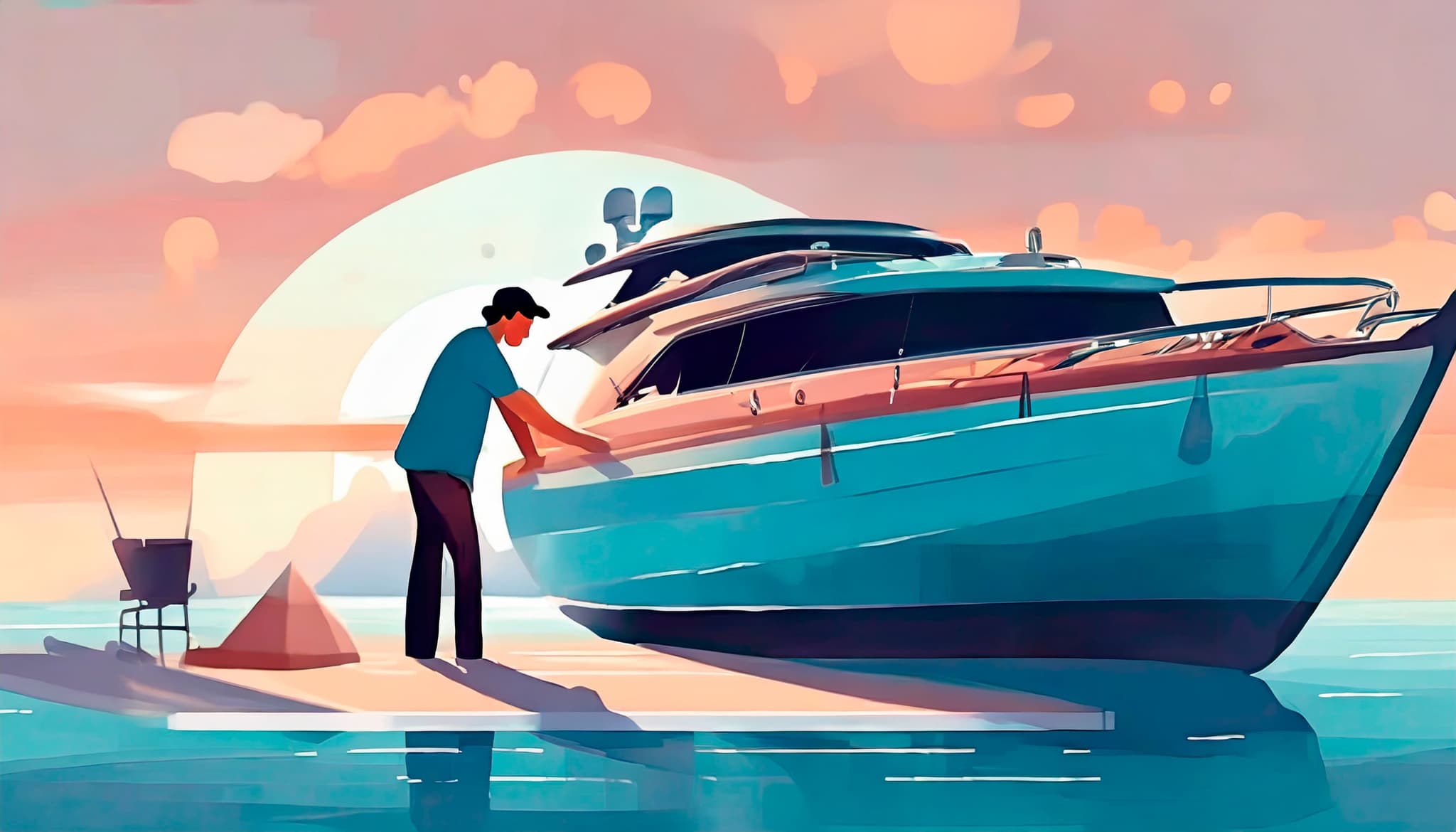
The final stretch in the journey of building a motorboat
The construction voyage concludes with finishing touches and stringent quality assurance. Aesthetic embellishments add personality, turning a boat into a unique marine masterpiece. Rigorous inspections and quality checks ensure every detail aligns with the design specifications and safety standards.
Once that's done, the motor yacht is carefully transported for its inaugural launch. Sea trials follow, testing the vessel under various conditions and leading to final adjustments, fine-tuning performance, and ensuring seaworthiness. The process culminates in the handover to the customer, where the manufacturer's painstaking craftsmanship transforms into the customer's joy and satisfaction, setting the stage for their maritime adventures.
The bottom line
How motorboats are made is an intricate blend of design, engineering, and craftsmanship, each stage imbued with precision and care. From the first sketch to the last aesthetic touch, every component is thoughtfully chosen and installed to create a vessel that marries functionality, safety, and style.
As intricate as they are resilient, these watercraft bear witness to countless hours of expertise and dedication. Therefore, when you next visit your local dealer, take a moment to appreciate the intricate ballet of construction that brought this marvel of marine engineering to life.
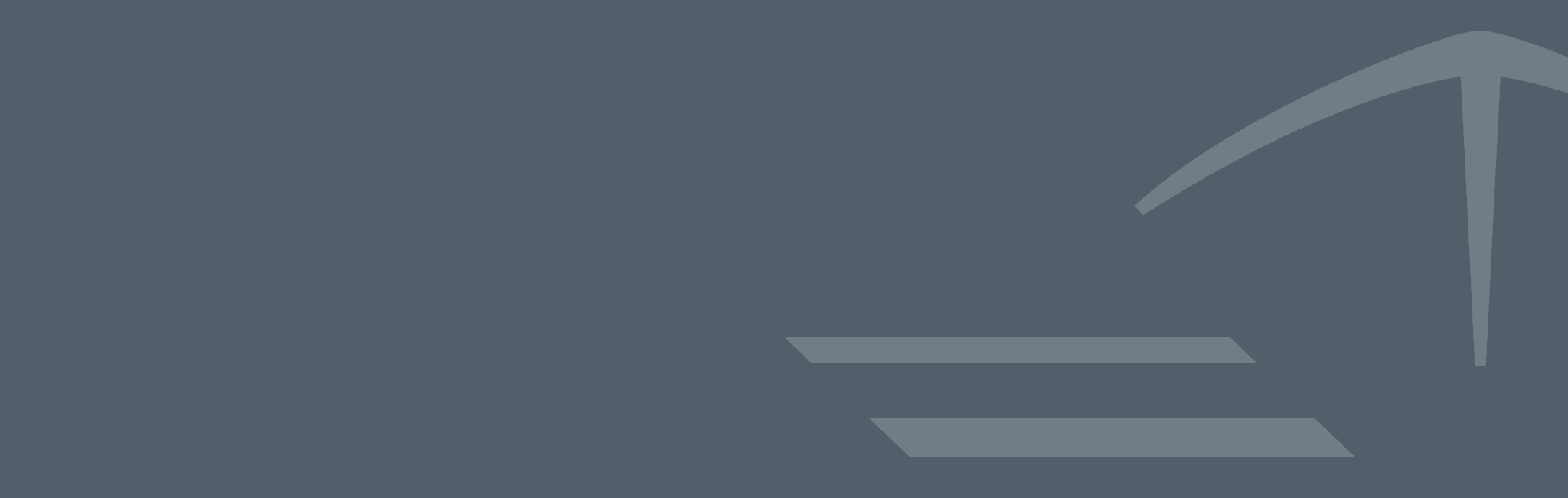